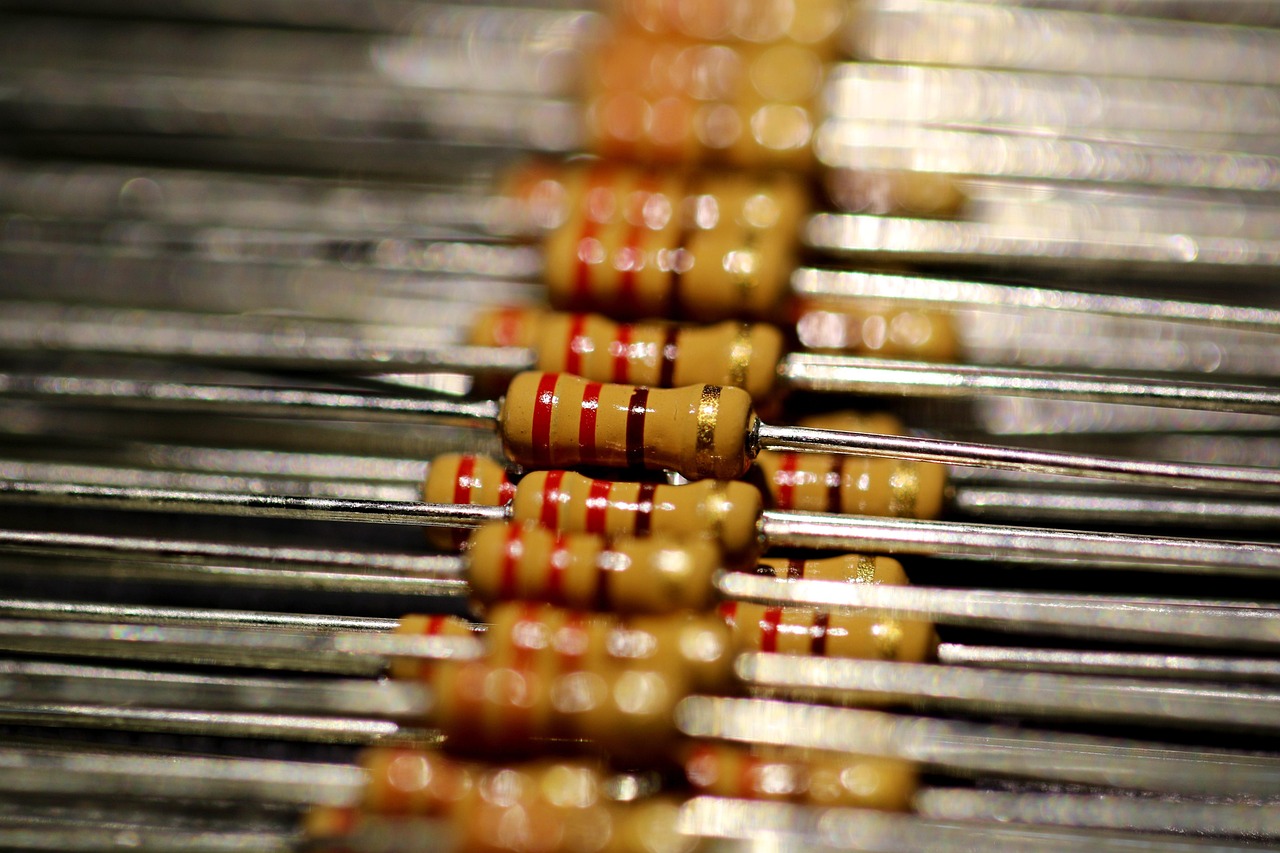
Choosing resistors for your next application comes with many considerations, including environmental, electrical, and mechanical. In this guide, we will look at some of these considerations, the types of resistors that exist, and why choosing the right one is so important.
The Importance of Consideration in Resistor Selection
Resistors—those tiny, color-banded cylinders that seem deceptively insignificant—are among the most fundamental components in electronics. They offer circuits the ability to resist current, drop voltage, and define electrical behavior across a wide array of designs. Whether you're managing power dissipation, controlling current through LEDs, or implementing voltage dividers for analog sensors, resistors are everywhere. Yet despite their simplicity, selecting the right resistor isn’t always as simple as checking the ohms on the schematic and calling it a day.
In a perfect, sterile lab environment with static temperatures and zero mechanical stress, sure—go ahead and grab the cheapest 10kΩ resistor you find in your parts bin. It’ll do the job just fine. But if you’re designing for the real world—the one outside the climate-controlled lab—things get messier. Cars vibrate like washing machines. Industrial settings deal with heat, dust, and sometimes corrosive fumes. Even consumer products get dropped, exposed to moisture, or sit under direct sunlight. The point is, your humble resistor is going to be exposed to some abuse, and not every resistor is cut out for that kind of life.
Let’s take a vehicle as an example. In an automotive environment, temperatures can swing from -40°C in the morning to 100°C under the hood by lunch. Add to that mechanical vibration, electrical noise, and intermittent power surges, and you’ve got a battlefield for components. A basic, off-the-shelf carbon film resistor might survive in your home thermostat, but put it in a brake controller, and you’re asking for a failure.
From an engineering standpoint, the consequences of using the wrong resistor can range from minor malfunction to catastrophic failure. Sensors can give inaccurate readings. Protection circuits can stop protecting. Power supplies can short or overheat.
But from a legal standpoint, things get a lot worse. If the device you're responsible for ends up causing property damage, injury, or worse—guess who’s in the firing line? Not the marketing team. Not the supplier. You, the engineer. Liability is real, and engineering negligence doesn’t look great in court.
So how does one choose the right resistor?
It starts with context. Understand the environment the component will operate in. Check temperature coefficients. Consider mechanical durability—thin-film vs thick-film, surface-mount vs through-hole. Think about power rating, tolerance, and even long-term stability under load. If you're working on a high-reliability or safety-critical application, you might need resistors rated for automotive or military standards. Those resistors aren’t just expensive for fun—they’ve been tested to survive conditions your average consumer-grade component simply won't.
And no, you’re not overthinking it. This is what separates a competent engineer from a hobbyist. Designing for real-world resilience is part of the job—and frankly, it’s what makes engineering fun. Every resistor tells a story. Just make sure yours isn’t a horror story waiting to happen.
Electrical Considerations — More Than Just Ohms
When it comes to choosing the right resistor, the first and most obvious place to start is the electrical specification. It might seem elementary, but you'd be amazed at how often engineers grab the first resistor that fits the schematic value without giving a second thought to the broader electrical demands. This isn't just about matching the color bands; it's about knowing exactly what kind of stress your component is going to face in the real world.
Ohmic value
The first, and most important, is choosing the right ohmic value. But selecting the correct value is the easiest and simplest part of resistor section.
Power Rating
The next consideration is the power rating of the resistor. While a little 1/16-watt resistor used to run a 2 mA status LED can work fine, that same resistor used to drop the voltage in series with a 10W motor circuit will result in catastrophe.
Every resistor dissipates power as heat, calculated by the good ol' formula:
P = I²R
If your resistor is rated for 0.25 W and you're asking it to dissipate 0.3 W, don't be surprised when it starts smelling funny—or worse, catching fire. Always add a bit of margin, and don’t push components to their rated limit unless you’re designing a product that’s meant to fail on purpose.
Voltage Rating
Then there’s voltage rating, which—granted—is often overlooked, and in many cases, that's fine. Most resistors are rated for voltages well above what they'll ever see in typical low-voltage electronics.
But get into high-voltage applications—say, anything north of 100 VDC—and suddenly dielectric breakdown becomes a real concern. Push a standard resistor too far, and the insulation or spacing between internal elements can fail.
That’s not just bad—it’s dangerously bad. For most designs, you're safe. For the 1% where this matters (medical, industrial, automotive), don't assume; check the datasheet.
Tolerance
And now, let’s talk tolerance. This is the percentage by which your resistor’s actual resistance can vary from its stated value—commonly ±5%, ±1%, or even ±0.1% in precision components. Depending on the application, this can either be a total non-issue or a critical design parameter.
If you're just setting the brightness of an LED, a 10% swing might be totally acceptable. But if you’re building a current sense amplifier or an analog sensor front-end, even a 1% variation might throw off your entire reading. Precision matters when accuracy is part of the spec.
So, to summarize:
-
Match resistance to the circuit’s needs.
-
Size for power, not just physical footprint.
-
Don’t ignore voltage ratings, especially in high-energy environments.
-
And when it comes to tolerance, be honest: are you building a toy, or something that someone's job—or life—might depend on?
Thermal Considerations — Heat Happens, Plan for It
Let’s get something straight: just because your resistor can handle the electrical load on paper doesn’t mean it’ll survive in practice. Temperature is the silent killer of components, and resistors are no exception. They may not move, click, or blink—but they definitely feel the heat.
Resistors generate heat as they dissipate power. This is a basic and unavoidable fact of Ohm’s Law and Joule’s Law doing their thing. But what many engineers forget is that a resistor’s performance is highly dependent on temperature. Even if it’s rated for 0.25 W and your circuit is pulling exactly that, the operating temperature of that resistor could still send it over the edge.
Temperature Coefficient
Enter the temperature coefficient of resistance (TCR). This spec tells you how much the resistance value drifts as temperature changes. It’s usually measured in ppm/°C (parts per million per degree Celsius), and depending on the resistor type, it can be anything from ±5 ppm/°C in precision metal film resistors to several hundred ppm/°C in cheaper carbon types.
That means a 1kΩ resistor with a TCR of 200 ppm/°C could shift by as much as 20Ω over a 100°C swing. Doesn’t sound like much? It is—especially in analog and sensing applications where even tiny shifts can throw off calibration or introduce unwanted offsets.
Non-Linear Thermal Drift
Worse still, thermal drift isn’t linear, and it’s not something most engineers budget for in a tight design timeline. But it should be, because the problem isn’t just the resistance drift—it’s the knock-on effects.
Imagine a feedback loop in a power supply drifting out of spec, or a precision analog sensor chain slowly creeping over temperature. These are problems that don’t announce themselves with a bang—they show up as unreliable behavior, phantom bugs, or products that “sometimes work.” That’s the stuff QA nightmares are made of.
Power Derating
Now let’s talk about power derating—something everyone nods at but few truly factor in. Resistor manufacturers don’t give you a flat power rating that applies across all conditions. That 0.5W rating you see in the datasheet? That’s typically valid at 25°C ambient. As the operating temperature rises, the maximum safe dissipation drops, often linearly. By the time you hit 125°C (which isn’t that extreme in automotive or industrial applications), your 0.5W resistor might only safely dissipate 0.2W—if you’re lucky. Ignore this, and you’re inviting thermal runaway, shortened lifespan, or outright failure.
So what’s the smart move?
-
Know your TCR. For precision circuits, choose low-drift resistors—metal film is a safe bet.
-
Derate aggressively. Don’t just meet the power rating, exceed it. Target 50–60% of rated power for continuous operation.
-
Account for environment. If you’re building for high-ambient conditions, calculate your worst-case thermals, and choose accordingly.
-
Use thermal vias or larger pads on your PCB to help dissipate heat—yes, layout does matter.
Mechanical Considerations — When Size (and Shape) Matters
Ask a junior engineer what resistor they used, and they’ll probably quote the resistance, the wattage, and maybe the tolerance if they’re feeling proud. Ask a senior engineer, and they’ll hit you with a full breakdown—including the mechanical footprint. Why? Because once you leave the simulation and start building real-world hardware, physical design constraints become just as critical as the electrical ones.
Size
Let’s start with the obvious: size matters. In today’s compact electronics, the physical dimensions of a resistor can make or break a layout—literally. Surface-mount resistors come in a variety of standard packages: 1206, 0805, 0603, 0402, 0201... and if you’re a real masochist, there’s 01005. Each smaller step saves precious board space, which might be the difference between fitting a design into an enclosure—or not.
Designing a smartwatch? Drone? Implantable medical device? You’re going to care a lot about component size. The 0805s might be easier to solder, but good luck cramming them into a millimeter-thick flex board. That’s where the 0402s and 0201s shine. They’re harder to work with, sure—but if your goal is ultra-compact, there’s no avoiding them. Just be aware that smaller parts often have lower power ratings and worse thermal handling, so there’s always a trade-off.
But we’re not just talking footprint. Resistors are 3D parts—they have height. Stack too many tall components on one side of the board and suddenly your product won’t close, or worse, your automated assembly process chokes on clearance issues. This is especially true in ultra-slim designs where even 0.5 mm can push you over mechanical tolerances.
Weight
And then there’s weight. Sounds trivial, right? What’s a 1/10th of a gram among friends? But multiply that by hundreds of components, and in the context of drones, RC vehicles, or space-limited automotive modules, it becomes a real concern. Excess mass leads to higher inertia, greater mechanical stress, and reduced efficiency over time. A microwave won’t care. But a drone fighting gravity every second of its flight? It absolutely will.
Mechanical Robustness
Also worth noting—mechanical robustness. Smaller resistors are more fragile. They’re more likely to crack under thermal or mechanical stress, especially during soldering or if the PCB flexes. Ever seen a hairline fracture on a 0402 resistor after someone twisted the board a bit too hard? It’s a silent killer—hard to detect, intermittent, and maddening to debug.
Here’s the quick checklist:
-
Choose the smallest size that still meets electrical and thermal requirements.
-
Be aware of component height—especially in enclosures with tight vertical tolerances.
-
Minimize unnecessary mass in mobile or airborne applications.
-
Consider mechanical stress—especially during manufacturing, handling, and deployment.
-
Use appropriate land patterns and soldering processes to avoid cracking or tombstoning.
Material Considerations — Not All Resistors Are Built the Same
We’ve talked voltage, current, heat, and even gravity. But one critical aspect still gets overlooked far too often: what the resistor is actually made of. It's easy to treat resistors as all being cut from the same cloth—but in reality, the material composition of a resistor has a major impact on its behavior, especially in precision and mission-critical applications.
Material Selection
Let’s start with the two big players in the resistor world: carbon film and metal film.
Carbon film resistors are cheap, widely available, and good enough for general-purpose use. But they come with baggage. Due to the granular structure of the carbon layer, the presence of impurities, and the inherently chaotic nature of carbon bonding, these resistors tend to generate more electrical noise. This is usually not a deal-breaker in basic circuits, like LED drivers or pull-down resistors. But in precision analog applications? Forget it.
If you're building sensor interfaces, op-amp feedback loops, or high-impedance analog paths, that noise matters. Which brings us to the superior alternative: metal film resistors.
Metal film resistors are laser-trimmed to tight tolerances and made using a uniform metal layer deposited on a ceramic substrate. This gives them not only better stability and lower temperature coefficients, but also significantly lower noise. Their clean, predictable behavior makes them the go-to choice for any circuit where accuracy and consistency matter. They cost more—but in engineering, you don’t cut corners where it counts. Use the cheap stuff in the blinkers; use the metal film in the brain.
Compliance & Regulation
Now, beyond electrical behavior, material matters for compliance as well. In sectors like aerospace, medical, and defense, material specifications can become downright militant. You’re not just designing for performance—you’re designing for regulatory survival.
Take flammability, for example. In aerospace, every component must comply with strict standards for flame retardance and smoke emission. That cheap off-the-shelf resistor from your favorite parts supplier? It might literally go up in flames during qualification testing. Specialized resistor types—such as flameproof metal oxide resistors—are specifically designed to pass these tests. They're bulkier and pricier, but that's the cost of safety and compliance.
And don’t forget corrosion resistance. Some environments are chemically hostile—marine, industrial, or medical sterilization processes. In such cases, materials with sealed construction or specialized coatings may be necessary to prevent degradation over time.
So, when picking a resistor, it’s not just about value, wattage, and footprint. Ask yourself:
-
Is electrical noise going to be a problem?
-
Does the application demand tight tolerances and low drift?
-
Are there any regulatory material requirements (flammability, toxicity, etc.)?
-
Will the resistor be exposed to corrosive or chemical environments?
Environmental Considerations — Your Resistor Doesn’t Live in a Vacuum
After all the careful thought that goes into resistance, power, thermal behavior, size, and materials, you might think your resistor selection process is finally done. But not so fast. None of that matters if the environment your resistor is deployed in chews it up and spits it out. Because while lab conditions are controlled and cozy, the real world is anything but.
Humidity
Let’s start with the quiet killer: humidity. Moisture in the air may seem harmless, but over time, it can seep into the resistor’s substrate, altering its electrical characteristics, increasing leakage, and slowly eroding any consistency you thought you had. In high-humidity environments, resistors without proper sealing will degrade, drift, and eventually fail.
Corrosion
And it doesn’t stop there. Corrosion is a very real and very common issue—especially in outdoor, marine, or industrial environments where moisture is paired with contaminants like salts, oils, and chemicals. Once corrosion sets in, the resistance value isn’t the only thing changing—so is the mechanical integrity. It’s a slow death, but one that can bring down entire circuits if ignored.
Pressure & Thermal Cycling
Next up: pressure and temperature cycling. In high-altitude or aerospace applications, pressure fluctuations can cause microcracks or delamination in poorly constructed resistors. Meanwhile, repetitive heating and cooling (think day-night cycles outdoors or repeated sterilization in medical gear) can induce thermal fatigue. These constant expansions and contractions, especially in dissimilar materials, can cause internal cracking or solder joint failures. Think of it like metal fatigue—but inside your components.
Vibration & Shock
Speaking of fatigue, mechanical vibration and shock are another silent threat—especially in automotive, aerospace, or industrial robotics. If your circuit is installed in a car engine bay or on a drone arm, it’s going to get shaken, rattled, and maybe even dropped. Resistors that aren’t built to withstand mechanical abuse will eventually crack or delaminate. That crack won’t show up in a visual inspection, but the moment your load spikes—it’s game over.
Compliance (RoHS & REACH)
And if you’re working in regulated industries like food processing or medical tech, you’ve got even more boxes to tick. Components need to comply with material safety and toxicity standards like RoHS (Restriction of Hazardous Substances) and REACH (Registration, Evaluation, Authorisation, and Restriction of Chemicals). These rules dictate what substances can and can’t be present—even in trace amounts. That cheap, lead-glazed resistor from an offshore vendor? Might be perfect electrically, but totally illegal (and potentially unsafe) for your application.
Unique Factors (Radiation etc.)
Finally, let’s talk radiation—not an everyday concern, but if you’re designing for space, nuclear environments, or high-altitude aviation, it suddenly becomes critical. Ionizing radiation can change the molecular structure of resistor materials, leading to drift or complete failure. In these cases, radiation-hardened resistors are the only choice. They're pricey and overkill for general electronics, but for satellites and orbital payloads, they’re non-negotiable.
Factors to consider
-
Humidity: Use sealed resistors for damp or high-moisture environments.
-
Corrosion: Avoid bare metal. Look for protective coatings and robust construction.
-
Thermal cycling: Choose resistors rated for wide temperature ranges with tested reliability.
-
Mechanical shock/vibration: Use ruggedized parts with verified mechanical durability.
-
Compliance: Always check RoHS/REACH for medical, food, or consumer applications.
-
Radiation: Use hardened parts in aerospace, defense, or high-radiation applications.
Supply Chain - Because “It Works” Isn’t the Same as “It Ships”
We’ve all been there—knee-deep in a design, finding that one perfect resistor that nails the spec sheet: power, tolerance, footprint, temp range. It’s flawless. And then you try to order it… and it’s either out of stock, obsolete, or only available from some vendor with a sketchy-looking website and a hotmail email address. Welcome to the supply chain side of engineering.
Resistors may be the most basic component in electronics, but that doesn’t mean you can just source them from anywhere. When your design uses hundreds—sometimes even thousands—of resistors, your choice of supplier, traceability, and certification matters just as much as the resistance value itself.
Cost
Let’s start with cost. When building at scale, every cent counts. A $0.02 price difference might not sound like much—until you’re buying 10,000 of them. That’s why many design engineers get pressure from purchasing teams to “just use the cheaper one.” And in some cases, that’s fine. But beware: not all resistors are created equal, and not all suppliers follow the same quality or traceability standards.
Standards
If you’re working in regulated industries—medical, automotive, aerospace—you’re not just buying a resistor, you’re buying into a supply chain compliance ecosystem. That means meeting standards like ISO 9001, having lot traceability, reliable documentation, material declarations (RoHS, REACH, etc.), and ideally, a supplier with a track record of consistent delivery.
Traceability
Sometimes the perfect part ticks all the electrical boxes, but when you look closer, it’s marked non-traceable or has no long-term stock visibility. That’s a red flag if your product is going into mass production, or needs to pass regulatory audit. You can’t just slap a replacement in later, because even subtle differences in construction or materials could change noise performance, thermal behavior, or mechanical reliability.
Vendor Reputation
Then there’s vendor reputation and logistics. A resistor from an obscure manufacturer might look great on paper, but what happens when the next batch fails incoming inspection? Or when a recall hits and you can’t trace which units were affected? If you don’t have supply chain traceability, you as the engineer may be liable for that oversight—especially in high-risk industries.
A few key takeaways:
-
Always spec parts from reputable suppliers with consistent availability and solid documentation.
-
Check compliance documentation (ISO, RoHS, REACH) early—don’t leave it to QA to flag it during pre-production.
-
Balance cost and availability with performance—if you can use a lower-cost resistor without compromising critical specs, do it. But do it knowingly.
-
Look for multiple sources for any part in your BOM, especially passive components. Second-source approvals can save a project when stock dries up.
-
Document your choices. If someone questions a resistor in a few months, you’ll want a paper trail.
Choosing a Good Supplier — Because Reliability Starts Long Before Your Circuit Powers Up
Trust, but verify. And ideally, buy from someone worth suing.
By now, we’ve established that resistors aren’t just tiny brown blobs with stripes—they’re mission-critical components that need to perform consistently, reliably, and compliantly in the real world. But even if you’ve nailed the electrical, thermal, mechanical, material, environmental, and regulatory specs, none of that means a thing if you can’t trust your supplier.
This is the part of the process where a little business sense goes a long way. Choosing a resistor isn’t just about the part—it’s about the company that stands behind it. And that decision can make or break your product.
Let’s start with the obvious: reputable component suppliers. Names like DigiKey, Mouser, RS, Farnell, and trusted OEMs like Vishay, Yageo, Panasonic, and TE Connectivity don’t just earn their status from flashy branding. They’ve built their reputation on decades of reliable fulfillment, repeat customer trust, and industry-standard quality control. When you buy from them, you’re buying into a support structure that includes datasheets, compliance documentation, traceability, and logistics that actually work.
Can you get a resistor from a no-name overseas vendor for half the price? Sure. Should you? Well, that depends on your goals. If you're prototyping or doing a one-off experiment, knock yourself out. Take the risk. Maybe save a few bucks. But if your design is headed for volume production, mass distribution, or any product with your name on it, now is not the time to cut corners.
And here’s the real kicker: right to recourse.
This is the concept that separates the real players from the hobby shop drop-shippers. Established suppliers often offer legal guarantees (explicit or implied through commercial terms) that let you hold them accountable for faulty components, incorrect material declarations, or traceability failures. If a batch of resistors fails in the field and costs your company thousands in recalls, you need to know you can escalate. File claims. Pursue damages. And get something back.
Smaller suppliers? Good luck. Even if you could take legal action, the costs of international litigation—especially with companies operating in less regulated jurisdictions—can far outweigh the cost of the components themselves. In most cases, you’re left eating the loss.
So what are the takeaways here?
-
Stick with reputable suppliers, especially when designing for production. Experience, customer support, and legal infrastructure are worth their weight in gold.
-
Use smaller suppliers for R&D and prototyping only, unless you’ve already validated their quality processes and supply chain reliability.
-
Look into legal coverage and supplier agreements. If you’re ordering large volumes, your company’s legal team should have a supplier contract that defines liability, traceability, and recourse in the event of failure.
-
Watch for grey market parts. Just because it looks like a Vishay resistor doesn’t mean it is one. Always source from authorized distributors.
-
Document your sourcing decisions, especially if your end product has compliance requirements or certification paths. Auditors and QA teams will want to know where those resistors came from.
Resistors — Simple Part, Serious Consideration
At first glance, selecting a resistor might seem like the most trivial part of a design. Just grab a standard SMD, 5% carbon film, slap it down, and call it a day—right? And truth be told, for 90% of applications, that approach works just fine. General-purpose digital circuits, indicator LEDs, pull-ups, and benign temperature environments won’t give you too much grief.
But engineering isn’t about designing for the 90%—it’s about knowing when you're in the critical 10%, and having the tools to make informed, reliable, and accountable decisions. Because when things go wrong—and they will—it’s never the flashy ICs or fancy power supplies that let you down. It’s always the humble little passive nobody double-checked.
Case in point: As I sit writing this, I’m working on an analog RF front-end that’s very vocal about not liking my resistor choices. And it took a seasoned RF engineer with decades of experience to spot the issue. Impedance mismatches, noise problems, thermal drift—it’s all there. And none of it would’ve been caught by a basic tolerance check or a surface-level datasheet skim.
So what’s the takeaway?
Use standard parts where you can, but understand your design's context. Know when you're dealing with RF, thermal extremes, mechanical stress, or compliance nightmares—and apply the principles we've discussed throughout this guide. Understand why each choice matters: the material, the environment, the thermal limits, the supplier, and yes, even the paperwork behind the part.
With this knowledge in hand, your next resistor selection won’t just be fast—it’ll be bulletproof.
Because in engineering, the best kind of resistor is the one you never have to think about again after you place the order.